Reckoned on a tonnage basis, tool steel represents only a few percent of the
total quantity of steel produced but its importance to the industry as a
whole is immense. Regrettably this fact is seldom sufficiently appreciated.
Perhaps in greatest measure this applies to the heat treatment of tool steel.
The cost of the steel and its heat treatment amounts generally to less than a
quarter of the total cost of the whole tool. A wrong choice of steel or
faulty heat treatment may give rise to serious disruption of production and
higher costs.
In this text, an example is tool steel W1, designated only by the type letter
and numeral as used in the USA and the UK for standardized tool steels. This
designation system is so well known by steel consumers all over the world
that no qualifying institutional designations are necessary.
Carbon steels and vanadium-alloyed steels
The hardening of these steels, which are made with carbon contents between
0,80% and 1,20%, is quite straightforward: Since the rate of carbide
dissolution proceeds rapidly, the holding time, as a consequence, is short
and therefore the heating of small tools can often take place without any
extra precautions against atmospheric oxidation.
The hardening temperature is about 780°C. Quenching is carried out direct
into brine with tempering following immediately. The quenching operation is
the most critical part of the heat treatment since too slow a rate of cooling
might give rise to either soft spots or quenching cracks.
If the tool is designed to contain hardened areas around holes or reentrant
angles the cooling effect must be very intensive at these areas. Manual
stirring will often suffice but in many cases the coolant must be sprayed on
to the tool. For sections heavier than 20 mm the depth of hardening, i.e. the
distance from the surface to the 550 HV level, is about 4 mm. Sections less
than about 8 mm in thickness will harden through.
For awkward tools, hardenability may be a crucial factor and under such
circumstances the composition of the steel must be adjusted in accordance
herewith, in particular as regards the alloying elements Mn and Cr, which
have a powerful influence on hardenability.
The diagram in Figure 1 shows how the hardening temperature affects the
depth of hardening and fracture number on Wl-type steel of conventional
composition. The V-content is only 0,04%, which implies that the steel
starts to be coarse-grained when the hardening temperature exceeds 815°C.
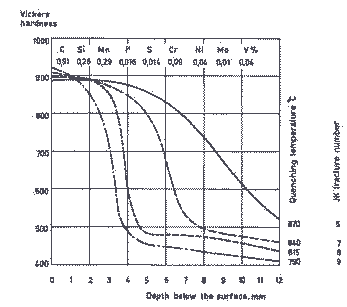
Figure 1.
|
Depth of hardening for carbon steel, 25 mm in diameter, corresponding to W1. Quenched in water from various temperatures
|
In Figure 2 are shown the results of corresponding trials with steel
containing somewhat larger amounts of alloying elements. The depth of
hardening is considerably greater. Owing to the high content of V the steel
remains fine-grained even when hardened from exceptionally high temperatures.
The very considerable toughness inherent in plain-carbon steel, due to its
shallow-hardening properties, is forfeited if the tool through-hardens
locally at some sections because the cross-sectional area there is too small.
For shearing tools or small tools generally, such as scissors, knives or
letter die punches, which are not subjected to heavy impact blows, this
drawback is of less importance. Tools operating under heavy blows, e.g.
upsetting dies for cold-heading of bolts, must not be through-hardened.
Coining and striking punches are other examples of carbon tool steels that
require high wear resistance. Such tools may also be subjected to bending
stresses and should therefore not be through-hardened. The tempering
temperature normally used for tools belonging to this group lies in the
range 170°C, the hardness being generally about 60-64 HRC. Representative
examples of tools made from grade W1 are shown in Figure 3.
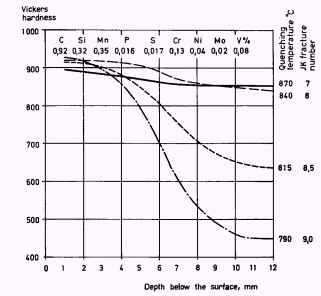
Figure 2.
|
Depth of hardening for carbon steel, 25 mm in diameter, corresponding to W1. Quenched in water from various temperatures
|
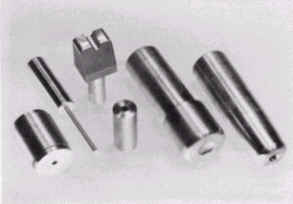
Figure 3. Punches made from steel W1
List of Articles - Knowledge Base