Carbon steels contain only carbon as the principal alloying
element. Other elements are present in small quantities,
including those added for deoxidation. Silicon and manganese
in cast carbon steels typically range from 0.25 to about
0.80% Si, and 0.50 to about 1.00% Mn.
Carbon steels can be classified according to their carbon
content into three broad groups:
- Low-carbon steels: < 0.20% C
- Medium-carbon steels: 0.20 to 0.50% C
- High-carbon steels: > 0.50% C
Low-alloy steels contain alloying elements, in addition to
carbon, up to a total alloy content of 8%. Cast steels
containing more than the following amounts of a single
alloying element are considered low-alloy cast steels:
Element
|
Mn
|
Si
|
Ni
|
Cu
|
Cr
|
Mo
|
V
|
W
|
Amount (%)
|
1.00
|
0.80
|
0.50
|
0.50
|
0.25
|
0.10
|
0.05
|
0.05
|
For deoxidation of carbon and low-alloy steels, aluminum,
titanium, and zirconium are used. Aluminum is more frequently
used because of its effectiveness and low cost. Unless
otherwise specified, the normal sulphur limit for carbon and
low-alloy steels is 0.06%, and the normal phosphorus limit is
0.05%.
Structure and Property Correlations
Carbon steel castings are produced to a great variety of
properties because composition and heat treatment can be
selected to achieve specific combinations of properties,
including hardness, strength, ductility, fatigue resistance,
and toughness. Although selections can be made from a wide
range of properties, it is important to recognize the
interrelationships among these properties.
For example, higher hardness, lower toughness, and lower
ductility values are associated with higher strength values.
The relationships among these properties and mechanical
properties will be discussed in the following text. Property
trends among carbon steels are illustrated as a function of
the carbon content in Fig. 1.
Strength and Hardness. Depending on alloy choice and
heat treatment, ultimate tensile strength levels from 414 to
1724 MPa can be achieved with cast carbon and low-alloy
steels. For carbon steels, the hardness and strength values
are largely determined by carbon content and the heat
treatment.
Figure 1: Properties of cast carbon steels as a
function of carbon content and heat treatment. (a) Tensile
strength and reduction of area; (b) Yield strength and
reduction of area; (c) Brinell hardness; (d) Charpy V-notch
impact energy
Strength and Ductility. Ductility depends greatly on
the strength, or hardness, of the cast steel (Fig. 2). Actual
ductility requirements vary with the strength level and the
specification to which steel is ordered. Quenched-and-tempered
steels exhibit higher ductility values for a given yield
strength level than normalized, normalized-and-tempered, or
annealed steels.
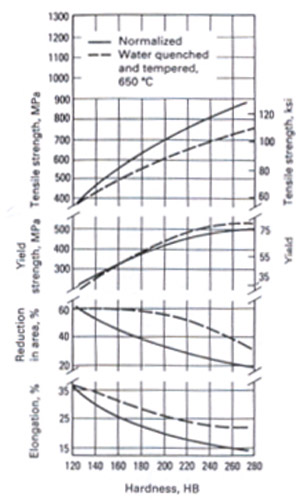
Figure 2: Tensile properties of cast carbon steels as
a function of Brinell hardness.
Strength and Toughness. Several test methods are
available for evaluating the toughness of steels or the
resistance to sudden or brittle fracture. These include the
Charpy V-notch impact test, the drop-weight test, the dynamic
tear test, and specialized procedures to determine
plane-strain fracture toughness.
Charpy V-notch impact energy trends at room temperature
reveal the distinct effect of strength and heat treatment on
toughness. Higher toughness is obtained when steel is quenched
and tempered, rather than normalized and tempered. Quenching,
followed by tempering, produces superior toughness as
indicated by the shift of the impact energy transition curve
to lower temperatures.
Nil ductility transition temperatures (NDTT) ranging from
38°C to as low as -90°C have been recorded in tests
on normalized-and-tempered cast carbon and low-alloy steels
in the yield strength range of 207 to 655 MPa. When cast
steels are quenched and tempered, the range of strength and
of toughness is broadened. Depending on alloy selection,
NDTT values of as high as 10°C to as low as -107°C can
be obtained in the yield strength range of 345 to 1345 MPa.
An approximate relationship exists between the Charpy V-notch
impact energy temperature behavior and the NDTT value. The
NDTT value frequently coincides with the energy transition
temperature determined in Charpy V-notch tests.
Plane-strain fracture toughness (KIc) data for a
variety of steels reflect the important strength-toughness
relationship. Fracture mechanics tests have the advantage
over conventional toughness tests of being able to yield
material property values that can be used in design
equations.
Strength and Fatigue. The most basic method of
presenting engineering fatigue data is by means of the S-N
curve, which relates the dependence of the life of the fatigue
specimen in terms of the number of cycles to failure N to the
maximum applied stress. Other tests have been used, and the
principal findings for constant amplitude tests and fatigue
notch sensitivity for cast carbon steels are highlighted
below.
The endurance ratio (endurance limit divided by the tensile
strength) of cast carbon and low-alloy steels as determined
by rotating-beam bending fatigue tests is generally taken to
be approximately 0.40 to 0.50 for smooth bars. The results
indicate that this endurance ratio is largely independent of
strength, alloying additions, and heat treatment.
The fatigue notch sensitivity factor determined in
rotating-beam bending fatigue tests is related to the
microstructure of the steel (composition and heat treatment)
and the strength. The quenched-and-tempered steels with a
martensitic structure are less notch-sensitive than the
normalized-and-tempered steels with a ferrite-pearlite
microstructure.
Section Size and Mass Effects. Mass effects are common
to steels, whether rolled, forged, or cast, because the
cooling rate during heat treating varies with section size
and because the microstructure constituents, grain size, and
nonmetallic inclusions increase in size from surface to
center. Mass effects are metallurgical in nature and are
distinct from the effect of discontinuities, which are
discussed in the following section in this article.
The section size or mass effect is of particular importance
in steel castings because mechanical properties are typically
assessed from test bars machined from standardized coupons
having fixed dimensions and are cast separately from or
attached to the castings. The removal of test bars from the
casting is impractical because removal of material for testing
would destroy the usefulness of the component.
Test specimens removed from a casting will not routinely
exhibit the same properties as test specimens machined from
the standard test coupon designs for which minimum properties
are established in specifications. The mass effect discussed
above, shows that the difference in cooling rate between the
test coupons and the part being produced, is the fundamental
reason for this situation. Several specifications such as ASTM
E 208, A 356, and A 757 provide for the mass effect by
permitting the testing of coupons that are larger than normal
and that have cooling rates more representative of those
experienced by the part being produced.
List of Articles - Knowledge Base